High Pressure Die Casting Products: Revolutionizing Metal Fabrication
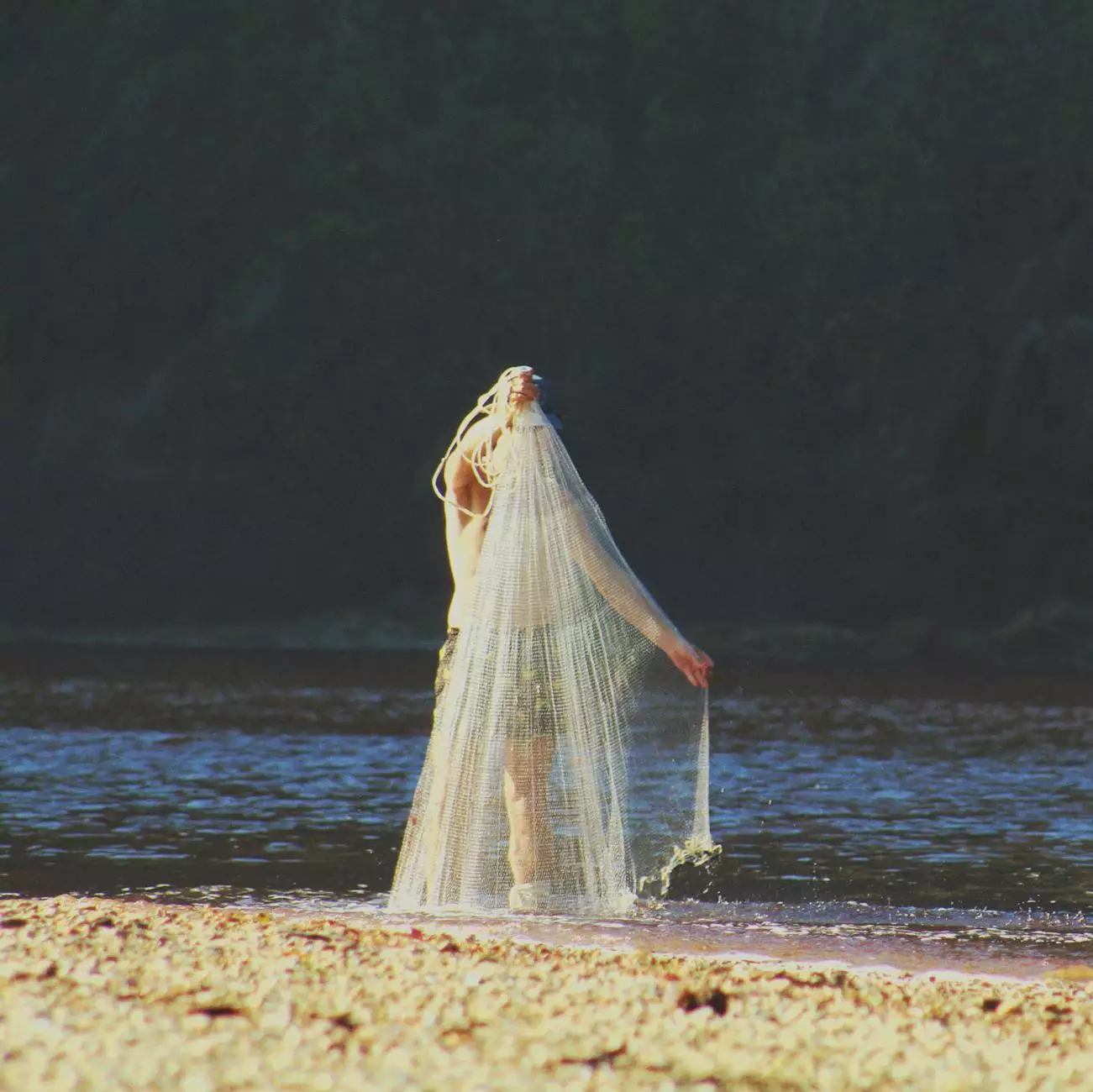
High pressure die casting products are at the forefront of modern manufacturing, offering unparalleled precision and efficiency in metal fabrication. This article delves into the intricacies of high pressure die casting, the benefits it provides to various industries, and how businesses like Deep Mould set the benchmark for quality and innovation in this field.
The Basics of High Pressure Die Casting
High pressure die casting is a process that involves injecting molten metal into a mold under high pressure. This method is widely used for producing complex shapes and components with high accuracy. The primary materials used in this process include zinc, aluminum, and magnesium alloys. Here’s a breakdown of how the process works:
- Melt Preparation: The chosen metal is heated until it reaches a molten state.
- Injection: The molten metal is injected into a pre-heated die under high pressure, ensuring that it fills every cavity of the mold.
- Cooling: Once the mold is filled, the metal is allowed to cool and solidify.
- Ejection: After solidification, the mold opens, and the newly formed product is ejected.
- Finishing: The ejected product may undergo additional finishing processes to enhance its surface quality and dimensional accuracy.
Advantages of High Pressure Die Casting Products
The adoption of high pressure die casting products brings a multitude of benefits to manufacturers and industries:
- High precision: The method allows for tight tolerances and complex geometries, making it ideal for intricate designs.
- Cost-effective: Mass production reduces per-unit costs significantly, making it financially viable for large-scale manufacturing.
- Material efficiency: The process minimizes waste, with a higher yield of usable parts compared to traditional methods.
- Excellent surface finish: The products often require minimal finishing, resulting in lower production times and costs.
- Versatility: High pressure die casting can accommodate various materials and is suitable for diverse applications.
Applications of High Pressure Die Casting Products
High pressure die casting finds applications across numerous sectors. Here are some key areas where this technology excels:
Aerospace Industry
In the aerospace sector, weight reduction is critical while maintaining structural integrity. High pressure die casting provides lightweight, durable components that contribute to fuel efficiency and performance.
Automotive Manufacturing
Automotive manufacturers leverage high pressure die casting products for engine blocks, transmission housings, and other critical components, ensuring reliability and performance in demanding environments.
Electronics
With the rise of electronic devices, die casting provides enclosures and heat sinks that meet the stringent requirements of the electronics industry. The precision offered by this process helps in creating compact and efficient designs.
Why Choose Deep Mould for High Pressure Die Casting?
As a leader in the metal fabrication industry, Deep Mould stands out for its commitment to quality and customer satisfaction. Here’s why partnering with Deep Mould is a smart choice for businesses looking for high pressure die casting solutions:
Expertise and Experience
With years of experience in the field, Deep Mould has perfected its processes to deliver outstanding results. Our team of experts understands the unique requirements of various industries and applies this knowledge to ensure optimal results.
Advanced Technology
At Deep Mould, we utilize state-of-the-art equipment and technology in our high pressure die casting processes. This not only enhances the quality of our products but also increases efficiency and reduces turnaround times.
Customization and Flexibility
We offer tailored solutions to meet the specific needs of our clients. Whether you require standard components or custom-designed products, Deep Mould is here to deliver.
Commitment to Quality
Quality control is paramount at Deep Mould. We adhere to strict quality standards at every stage of production, ensuring that our high pressure die casting products meet or exceed industry benchmarks.
Future Trends in High Pressure Die Casting
The future of high pressure die casting is promising, with several trends set to shape the industry:
- Increased automation: The integration of automation and robotics will streamline production processes, improving efficiency and reducing labor costs.
- Sustainable practices: Manufacturers are increasingly focusing on sustainability, adopting eco-friendly materials and recycling practices in die casting operations.
- Advanced materials: The exploration of new alloys and materials will expand the applications for high pressure die casting beyond traditional sectors.
- Enhanced simulation technologies: The use of simulation software will allow manufacturers to predict outcomes and optimize die designs before production begins.
Conclusion: The Impact of High Pressure Die Casting Products
In summary, high pressure die casting products are transforming the landscape of metal fabrication, offering precision, efficiency, and cost-effectiveness. With industry leaders like Deep Mould pushing the boundaries of innovation and quality, the future of die casting looks bright. Businesses that embrace this technology will not only enhance their product offerings but also improve their competitive edge in an ever-evolving market.
For those interested in exploring high quality high pressure die casting solutions, look no further than Deep Mould. Our expertise, advanced technology, and commitment to excellence will ensure that your business achieves its goals.