Understanding **Instrument Pipe Fitting**: A Comprehensive Guide
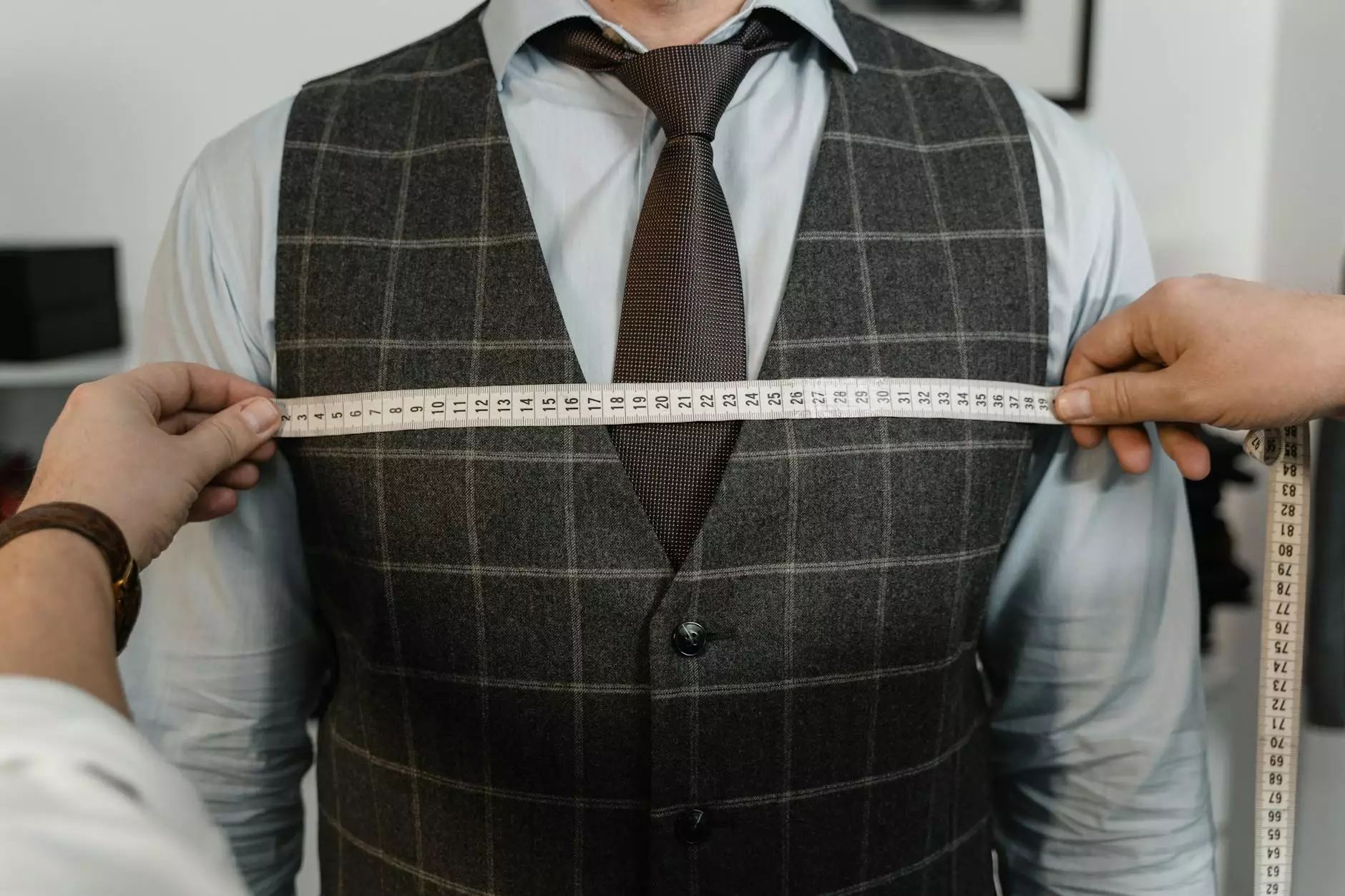
In the intricate world of engineering and industrial operations, instrument pipe fitting holds a crucial position. This article delves into the fundamentals, applications, types, and best practices associated with instrument pipe fittings, particularly focusing on how Fitsch.cn contributes to this essential aspect of various industries through superior products and services.
The Importance of Instrument Pipe Fitting
Instrument pipe fittings are vital components in an array of systems that involve fluid and gas flow management. They are designed to connect different sections of piping systems, providing functionality such as:
- Fluid Control: Regulating the flow and pressure of liquids and gases.
- System Integrity: Ensuring the robustness of piping systems against leaks.
- Ease of Maintenance: Facilitating easier inspections and repairs.
- Safety Compliance: Meeting industry standards to ensure workplace safety.
Types of Instrument Pipe Fittings
There are numerous varieties of instrument pipe fittings, each tailored for specific applications:
1. Elbows
Elbows are used to change the direction of the pipe. Available in 45° and 90° angles, they help in routing the pipelines through various structures while avoiding obstacles.
2. Tees
Tees are used to branch out from a main pipeline. They allow for measurements to be taken from one line to another without disrupting the flow.
3. Reducers
This type of fitting enables the transition between two pipes of different diameters, ensuring a smooth flow of materials while maintaining system pressure.
4. Caps and Plugs
Caps and plugs are essential for sealing the ends of pipes, effectively blocking off flow when necessary or when extending the piping system is not in immediate plans.
5. Flanges
These components are utilized for connecting pipes, fittings, and valves, making them indispensable in assemblies where disassembly is required for maintenance or inspection.
Materials Used in Instrument Pipe Fittings
The choice of materials for instrument pipe fittings is pivotal to ensure durability and resistance to corrosive elements. Common materials include:
- Stainless Steel: Highly resistant to corrosion, making it ideal for chemical applications.
- Carbon Steel: Most commonly used due to its toughness and strength.
- Copper: Excellent thermal conductivity, often used in plumbing and refrigeration systems.
- Plastic Composites: Lightweight and resistant to corrosion, used in specific chemical contexts.
Applications of Instrument Pipe Fitting Across Industries
Instrument pipe fittings serve critical roles across diverse sectors, including:
1. Oil and Gas
In the oil and gas industry, fittings facilitate the transportation of substances under high pressure, ensuring safety and operational efficiency.
2. Chemical Processing
Used for transferring corrosive fluids and gases, instrument pipe fittings in chemical plants are critical for both operational safety and procedural effectiveness.
3. Water Supply and Wastewater Treatment
In municipal water systems, these fittings ensure a steady flow while maintaining water quality through proper design and material selection.
4. Pharmaceutical Manufacturing
The pharmaceutical industry employs instrument pipe fittings to transport and process sensitive bio-fluids, requiring compliance with strict sanitary standards.
5. Food Processing
Likewise, in food processing, fittings are designed for cleanliness and hygiene to prevent contamination while maintaining product integrity.
Choosing the Right Instrument Pipe Fitting
Selecting the appropriate instrument pipe fitting is crucial for ensuring operational success. Here are some key factors to consider:
- Operating Pressure: Understand the pressure requirements of your system to select fittings that can sustain it.
- Corrosiveness of Fluids: Choose materials that are compatible with the substances being transported.
- Temperature Variations: Consider how temperature fluctuations can affect material performance.
- Connection Type: Ensure compatibility with existing piping systems, whether threaded, welded, or flanged.
Best Practices in Instrument Pipe Fitting Installation
Proper installation of instrument pipe fittings is essential to guarantee system integrity and safety. Here are several best practices:
1. Thorough Inspection
Before installation, inspect both the fittings and the associated pipes for any signs of damage or wear. This step is critical to prevent future failures.
2. Use of Proper Tools
Utilize appropriate tools for installation. Using the wrong tools can damage fittings and lead to leaks or pipe failures.
3. Follow Manufacturer Guidelines
Always adhere to the manufacturer's specifications and instructions for installation, as they provide necessary details specific to the fittings being used.
4. Pressure Testing
Perform pressure tests after installation to check for leaks, ensuring that everything functions as expected before the system goes operational.
Conclusion
The significance of instrument pipe fittings in various industries cannot be overstated. Their role in ensuring safe, efficient, and reliable fluid transfer is paramount. Whether in the oil and gas sector, chemical processing, or even food production, the demand for quality fittings like those offered on Fitsch.cn remains high. By understanding the various types, materials, and installation practices, businesses can enhance their operational efficiency and maintain compliance with safety standards. Investing in high-quality instrument pipe fittings ensures not only the success of current projects but also safeguards future expansion and innovation.